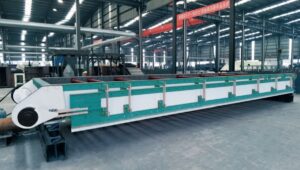
Sreader is a high-end brand in the screening domain, meticulously developed for China University of Mining and Technology and Henan Zhenyuan Technology Co., Ltd. Its screening theory and technology, originating from Germany, are world-leading and uniquely domestic, revolutionizing the traditional screening theories and technologies in China.
With a national-level professional technical R&D team in the field of vibration utilization, Srid ensures its screening technology remains at the forefront of wet and sticky material processing and deep screening through continuous innovation. The mechanical flip-flow screen, jointly developed with China University of Mining and Technology, has undergone a full lifecycle process including theoretical design, mechanical vibration simulation design with ADAMS, finite element structural analysis with ANSYS, prototype manufacturing, and market launch of industrial-grade products. The final practical data demonstrates that this type of flip-flow screen has set new records in the performance of wet and sticky material processing and deep screening, filling the gap in the field of deep screening!
Sreader has long been committed to the research of wet and sticky material processing and deep screening technologies, successfully applying advanced German screening theories and technologies to industries such as coal preparation plants, coal chemical industry, fertilizer plants, construction aggregates, and non-ferrous metals. The mechanical flip-flow screen is a typical application of Sreader's screening technology, with its efficient and excellent screening efficiency and reliable equipment characteristics reflecting the continuation of German quality.
Practice effect
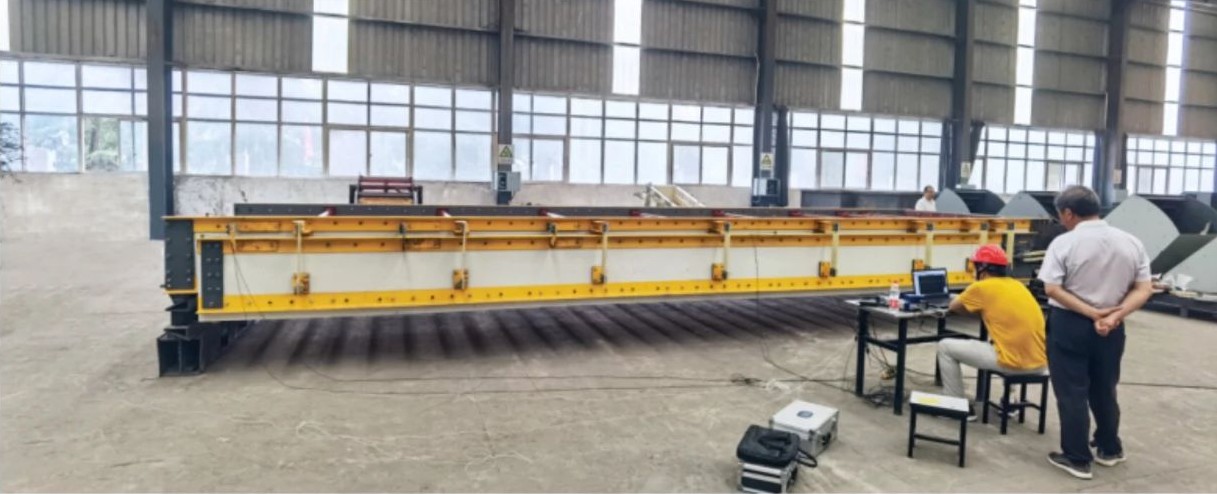
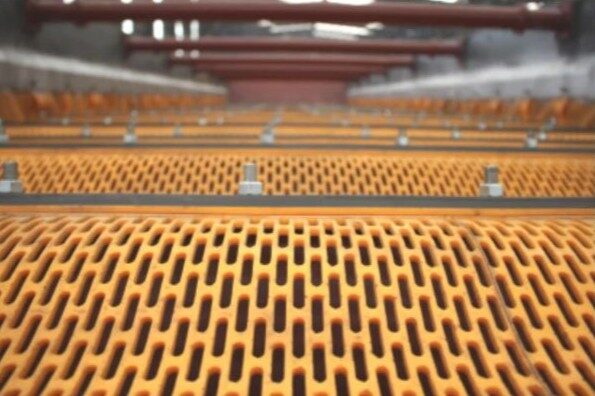
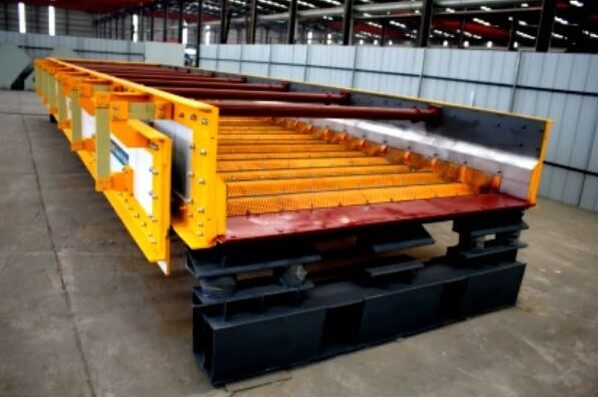
Applications in Other Industries: The sand and gravel aggregate industry, non-ferrous metals industry, and particularly the rapidly developing aggregate industry, where the screening of 3-5mm wet and sticky materials remains a persistent challenge. The application of mechanical flip-flow screens will address current industry difficulties and promote industry development.
Years of domestic practical testing have proven that mechanical vibrating flip-flow screens have unparalleled advantages in the field of fine screening (especially for damp and sticky materials), solving problems that have plagued the industry for years and providing a solution for all-weather fine particle screening. Since 1998, the Yima Coal Industry and Gasification Plant in Henan have been using mechanical flip-flow screens that have been running well to this day. Nearly 25 years of continuous operation demonstrate the superiority of the equipment's structure, with almost no spare parts consumption other than the screen panels during operation, showcasing high reliability and low maintenance costs. To date, several production units are experiencing the significant benefits it brings!
Case Study: The Shenhua Wanli No.1 Mine and Lijiahao Coal Mine of the National Energy Group originally used post-screening methods for 6mm fine screening. During use, they encountered industry problems such as hole clogging and material caking, which severely constrained production due to the inability to perform deep classification. After adopting mechanical flip-flow screening technology, practical verification has shown that this screening technology has solved the fine screening industry's problems, addressing the industry's difficulties and pain points!
Differences in Vibrating Screens
Category | Mechanical Flip-Flow Screen | Vibratory Flip-Flow Screen | Traditional Vibrating Screen |
Working Principle | Driven by a crank-link mechanism inside the drive unit, the inner and outer screen frames are propelled to produce linear reciprocating motion (without an exciter) | Evolved from traditional circular or linear vibrating screens, a single drive generates dual vibrations (excited by an exciter) | A single drive produces a single vibration (excited by an exciter) |
Working Amplitude | The relative amplitude of the inner and outer screen frames depends on the size of the eccentricity and is not affected by external factors such as material, thus the amplitude remains constant. | The amplitude is significantly influenced by the material; as the output of the screening machine increases, the amplitude value decreases accordingly, affecting the screening efficiency. | |
Screening Efficiency | The processing capacity per unit area is approximately 30% higher than that of vibrating flip-flow screens, with screening efficiency exceeding 95%. | ||
Screen Clogging | The constant flexing action of the elastic screen panels prevents particle adhesion. The extension of the screen panels causes a slight variation in the aperture opening in the tension direction, which can be described as the “breathing” of the screen apertures. Combined with high acceleration forces, this prevents particles close to the size of the apertures from clogging them. Vibratory flip-flow screens and traditional vibrating screens are prone to clogging when handling wet and sticky materials, making screening difficult. | ||
Screen Machine Reliability | Compared to the speed of traditional screening machines, mechanical flip-flow screens operate at a low speed of less than 600 rpm, with the machine itself generating stress from only about 2-3G of acceleration. Therefore, the screen machine inherently possesses higher reliability. Both theoretical design and practical testing have proven that similar products have undergone industrial durability verification. | ||
On-site Noise | Due to its low rotational speed and the absence of an exciter drive, the mechanical flip-flow screen operates with significantly lower noise levels compared to vibratory flip-flow screens and traditional vibrating screens, enhancing the comfort of on-site workers. | ||
Maintenance | The screen machine is easy to maintain with fewer on-site wearable parts, requiring only regular lubrication and periodic replacement of the screen surface. | The rubber shear springs of vibratory flip-flow screens are prone to aging, leading to longer downtime for repairs; the maintenance costs for exciters are high. | |
Foundation Impact | The rubber springs supporting the screen machine bear only the weight of the machine in the vertical direction during operation and the inertial force of the machine in the direction of the installation angle. However, the low-speed characteristic of the screen machine results in no vertical impact on the foundation, reducing the foundation load requirements and additional investment. | Driven by the exciter, the screen machine generates a significant impact load on the foundation, requiring higher foundation load capacity and increasing additional investment. |